The global demand for electric vehicles (EVs) and their batteries is increasing as the prices of EV batteries continue to fall. The average price of a lithium-ion EV battery pack has decreased significantly from $1,200/kWh to $132/kWh since 2010. An EV battery pack comprises multiple interconnected modules that consist of tens to hundreds of rechargeable lithium-ion cells. These cells account for approximately 77% of the total cost of the average battery pack, which is around $101/kWh.
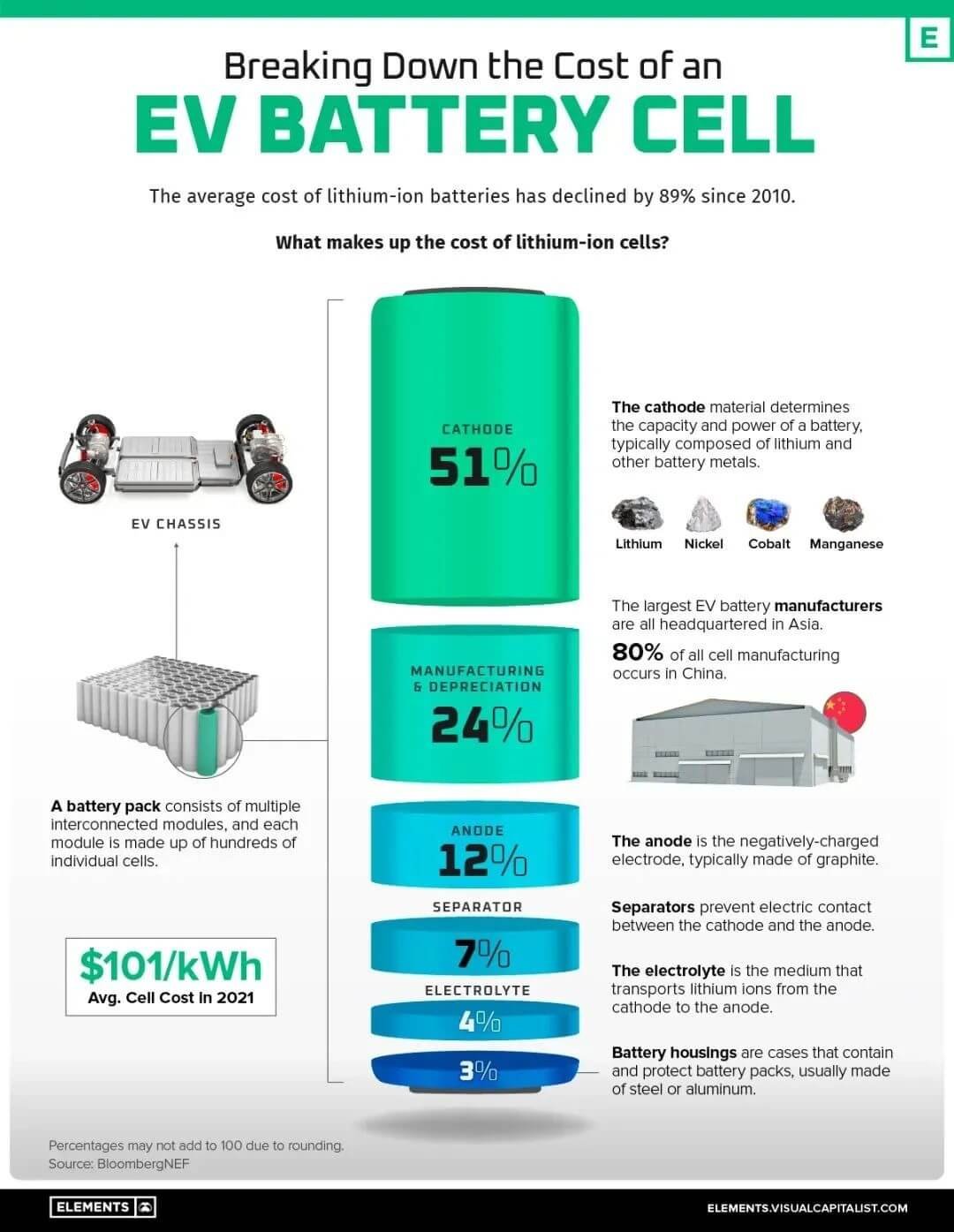
The Virtual Capitalist website has published an infographic that analyses the cost of electric vehicle power cells.
Electric vehicle battery components as a percentage of total battery pack cost:
- – Cathode 51 %
- – Cathode 51% Manufacturing and depreciation 24%
- – Anode 12%
- – Separator 7%
- – Electrolyte 4%
- – Other materials 3%
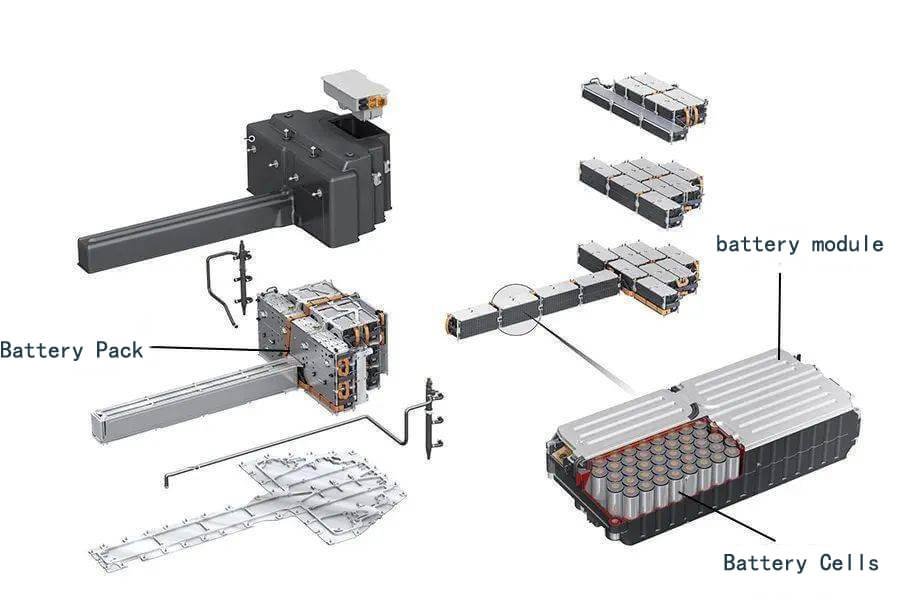
Why are cathodes so expensive?
The cathode serves as the positive electrode in a battery. During discharge, both electrons and positively charged lithium ions flow from the anode to the cathode, where they are stored until the battery is recharged. As a result, the cathode plays a crucial role in determining the battery’s performance, range, and thermal safety, as well as the overall performance of the electric vehicle. Therefore, it is one of the most critical components. Batteries are composed of refined metals, which vary depending on the battery chemistry. Typically, lithium and nickel are included.
Commonly used modern cathode compositions include:
- (NCA)- Lithium iron phosphate (LFP)
- – Lithium nickel manganese cobalt (NMC)
- – Lithium nickel cobalt aluminum oxide (NCA)
The cathode’s battery metals are in high demand, with automakers like Tesla rushing to secure supply. In fact, the metals in the cathode, along with those in the rest of the battery, account for about 40% of the total battery cost.
Components other than the cathode account for 49% of the battery cost.
The battery manufacturing process, which includes producing the electrodes and assembling and finishing the battery, accounts for 24% of the total cost. The anode is a crucial component of the battery, accounting for 12% of the total cost and approximately a quarter of the cathode. Typically, anodes for lithium-ion batteries are made from natural or synthetic graphite, which is less expensive than other metallic materials.
The heart of electric vehicles – power battery
The power battery is the primary system in new energy electric vehicles, serving as the power source. It accounts for 30% to 40% of the total vehicle cost and is a signature component that distinguishes it from traditional fuel vehicles. It is important to ensure that the power battery is functioning optimally to maintain the vehicle’s performance. In contrast, the engine is the heart of a traditional fuel vehicle.
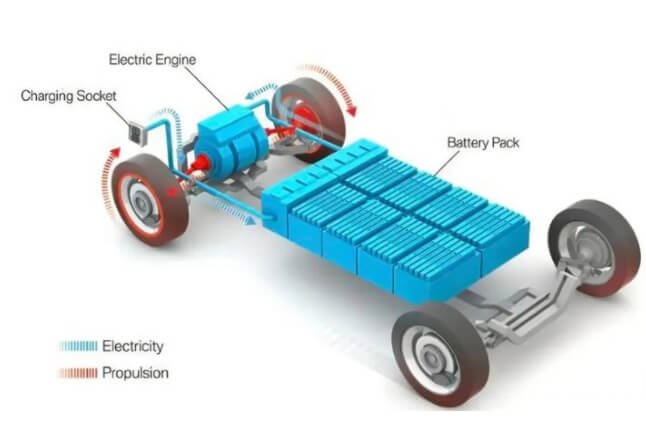
Currently, the future prospects of electric vehicles are uncertain due to occasional safety accidents, shortened winter range, and other factors. The main reasons for this skepticism are: limited range, safety concerns regarding power batteries, inconvenient charging, and battery recycling.
And these four issues put them down to one problem: the problem of the power battery.
Therefore, electric vehicles is a policy-oriented product, or the future can replace the fuel car, to meet the real market demand for the product of the key lies in the ability to solve the problem of the power battery?
Structural Composition of Power Battery
The power battery is composed of several battery cells, CSC information acquisition system, battery management control unit (BMU), battery high-voltage distribution unit, cooling system and so on.
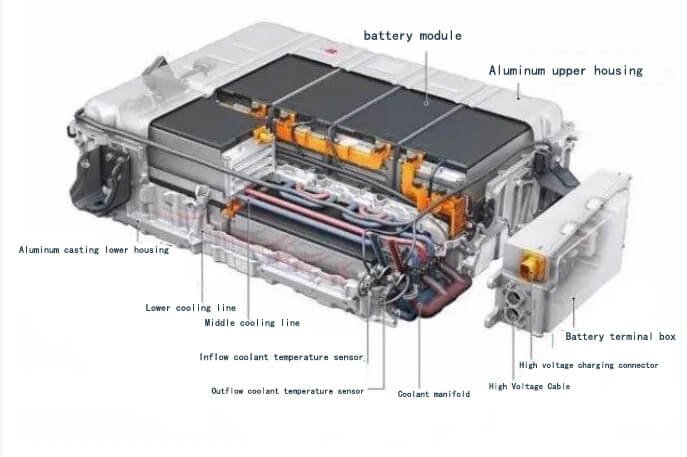
Automobile power battery unit
A battery monomer is the smallest unit that makes up a battery. It consists of a positive electrode, negative electrode, organic electrolyte, and other components. A battery module is formed by connecting several battery monomers in parallel. A battery unit is formed by connecting several battery packs in series, and a power battery assembly is formed by connecting several battery units in series. The current market power battery capacity is mainly provided by two types of batteries: ternary lithium and lithium iron phosphate. This article focuses on these two types of power batteries.
Power battery type 1. Ternary lithium battery
The ternary lithium battery uses lithium nickel cobalt manganese oxide (Li(NiCoMn)O2) or lithium nickel cobalt aluminate as its cathode material. The cathode material is a ternary composite containing nickel, cobalt, and manganese or aluminum. This type of battery is also known as a ternary polymer lithium battery. The cathode of the battery can be made using a ternary material whose ratio of nickel, cobalt, and manganese can be adjusted based on the actual requirements. This material is made using manganese salt as raw material. Ternary lithium batteries are high-energy lithium batteries that are relatively safer than cobalt lithium batteries. Lithium batteries are high-energy density and high-voltage energy storage devices that are widely used in mobile and wireless electronic equipment, power tools, hybrid and electric transportation, and other fields.
Car companies prefer ternary lithium batteries due to their high energy density. A higher energy density means that the battery can store more power per unit volume or weight.
This results in a longer range for pure electric vehicles. Therefore, the range advantage of lithium ternary batteries is attractive to electric vehicle enterprises that pursue long range. Ternary lithium batteries have an advantage in low temperature resistance. Compared to other types of batteries, they experience less power attenuation in the winter under the same low-temperature conditions. This makes them more suitable for cold northern regions.
Ternary lithium batteries have poor stability, which can lead to thermal runaway at temperatures between 250-350℃. There is also a high risk of spontaneous combustion during rapid charging. Therefore, these batteries require excellent heat dissipation performance, and the BMS battery management system must meet higher technical requirements.
Power battery type 2. Lithium iron phosphate battery
The lithium iron phosphate battery is a type of lithium-ion battery that uses lithium iron phosphate (LiFePO4) as the positive material and carbon as the negative material. It has a single rated voltage of 3.2V and is known for its high safety. Currently, lithium iron phosphate batteries have the best thermal stability, with a thermal runaway temperature generally above 500 degrees, resulting in a very low risk of battery spontaneous combustion. The cycle life of lithium iron phosphate batteries is relatively long, with the number of charge and discharge cycles greater than 3500 times before they start to decline, equivalent to 10 years. Additionally, lithium iron phosphate batteries are competitively priced.
Lithium iron phosphate batteries offer several advantages, including high operating voltage, High energy density, and longer cycle life, as well as good safety performance, low self-discharge rate, and no memory effect.
However, the energy density of lithium iron phosphate batteries is currently lower than that of lithium ternary batteries, with an average of 130-140Wh/kg compared to the average of 160Wh/kg for lithium ternary batteries. This makes it difficult to compare the range of the two types of batteries, and is also why lithium iron phosphate batteries are less commonly used in pure electric vehicles.
Power Battery Type 3. Hydrogen Fuel Cells
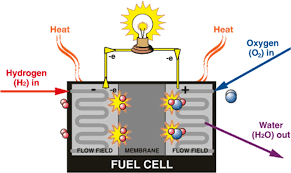
Compared to storage batteries, hydrogen fuel cells are a niche but truly zero-emission clean energy source. They convert the chemical energy of hydrogen and oxygen directly into electric power. The reverse reaction of water electrolysis is the basic principle. Hydrogen and oxygen are supplied to the cathode and anode respectively. Hydrogen diffuses outward through the cathode and electrolyte reaction occurs. Electrons are then released to reach the anode through the external load, resulting in the production of only water and heat.
Hydrogen fuel cells offer high energy conversion efficiency, as well as being pollution-free and noise-free. They are expected to be a key development direction for the future power battery industry. For instance, Hyundai recently announced a ‘2025 strategy’ that includes expanding sales of both pure electric and hydrogen-fueled electric vehicles. Furthermore, prominent car manufacturers such as Toyota and Honda are actively promoting the advancement of hydrogen fuel cell technology.
However, many of the problems with hydrogen-fueled electric vehicles have not yet been effectively solved. The main issue is the inconvenience of hydrogen storage, and the current cost is also too high.
The future development trend for power batteries is higher energy density, faster charging speed, stronger safety, and lower cost.